インテーレクチファイヤの自作・・・備忘録
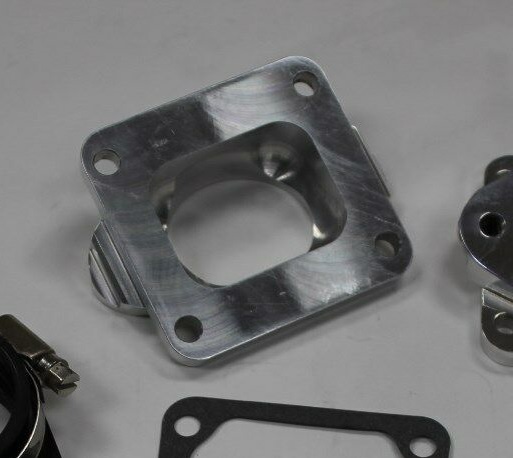
このままでは渦を巻いてしまうため必然的に制作中・・
流体エネルギーが安定する事でキャブレターベンチュリ内の吸気負圧にも影響が及ぶ事は間違いないと思われます?・・
因みに、2サイクルの吸気系チューニングパーツでは天才アイゼン・ボイセンが考案した究極の2サイクル吸気システム、ラドバルブは昔から有名。
因みに、2サイクルの吸気系チューニングパーツでは天才アイゼン・ボイセンが考案した究極の2サイクル吸気システム、ラドバルブは昔から有名。
効果については・・
春のRDミーティングに参加の道中、明らかに装着前と違いがあり充填効率の向上を感じられた事によるのだが・・
厳密にはパワーチェック等の方法を試さなければ効能を知る方法はないと思う?
結局の所 体感上から効果はあるのは間違いないと思うのである・・
春のRDミーティングに参加の道中、明らかに装着前と違いがあり充填効率の向上を感じられた事によるのだが・・
厳密にはパワーチェック等の方法を試さなければ効能を知る方法はないと思う?
結局の所 体感上から効果はあるのは間違いないと思うのである・・
RDミーティングまでの期間制作にあたっては 制作の手順~~材料の選定の工程が最も時間がかかってしまった・・
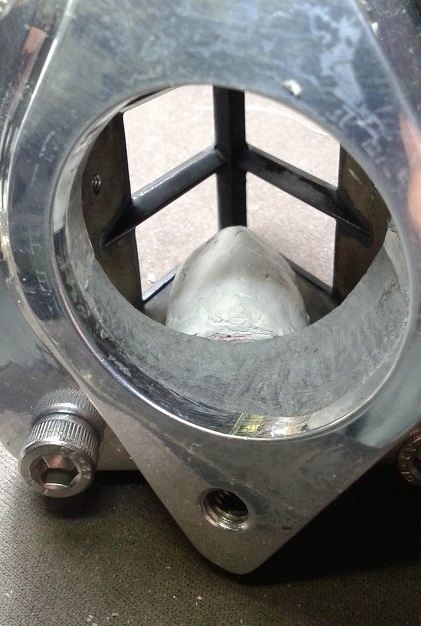
画像は流線形の型を作り インマニとの繋がりを確認しているところである・・
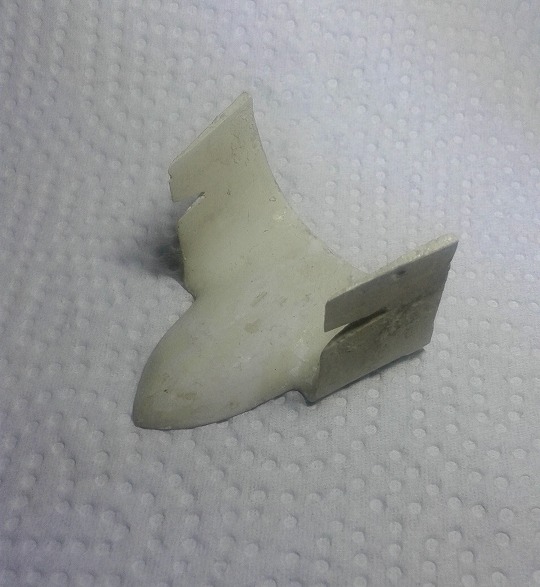
次に型を4個抜いて複製の後、リードバルブ内で二つの複製型を向い合せに連結し完成させる・・
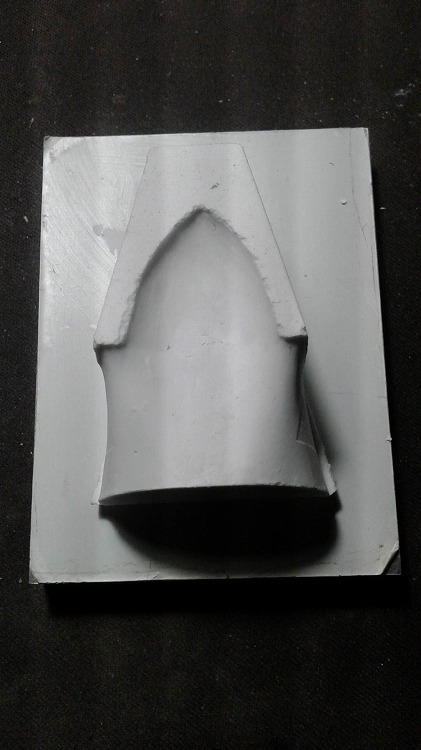
耐久性が無く4回の型抜きに耐えられない・・
粘土系は型が硬化する時間がかかりこれもダメ・・
低コストのつもりだったが、結局いろいろ買った時点でコストオーバー・・・
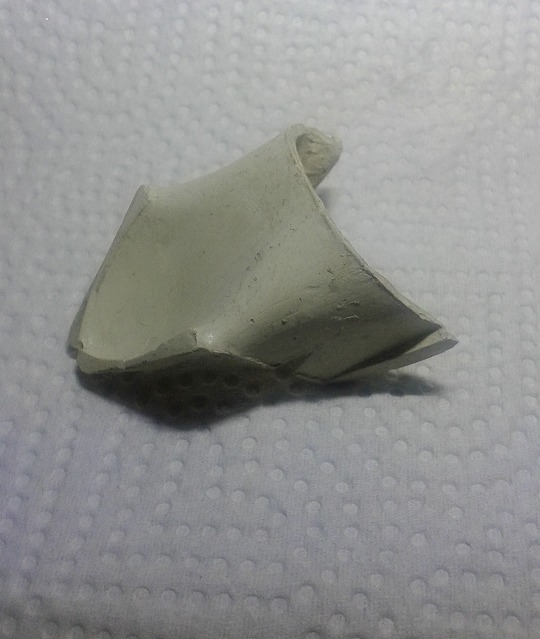
本体製作用パテの選定は セメダインののエポキシパテ金属用が低コストで硬化時間も最短で手待ち時間がかからず最適。
因みに、理型材はシリコンオイルを刷毛で型に塗っている。
因みに、理型材はシリコンオイルを刷毛で型に塗っている。
パテを錬っていると数分後には硬化が始まるため、少量を素早く寝り
型にパテを一方から押す様に隙間なく張込んでいくのだが
硬化が進むと内法などにパテを押し込む事が出来なくなってしまう。
よってパテの張り込みは少量を3~4回に分け型に盛って行く必要があり
素早く練り、素早くパテを型に確実に張り込まなければならない
感覚的には練りだしてから3分以内の作業と思う?
パテ盛り1回分の量を減らすと確実な作業と硬化時間とのバランスが良い。
だが、打ち継ぎ部分の処理をする事で後の作業が効率アップと仕上がりも良くなる。
型にパテを一方から押す様に隙間なく張込んでいくのだが
硬化が進むと内法などにパテを押し込む事が出来なくなってしまう。
よってパテの張り込みは少量を3~4回に分け型に盛って行く必要があり
素早く練り、素早くパテを型に確実に張り込まなければならない
感覚的には練りだしてから3分以内の作業と思う?
パテ盛り1回分の量を減らすと確実な作業と硬化時間とのバランスが良い。
だが、打ち継ぎ部分の処理をする事で後の作業が効率アップと仕上がりも良くなる。
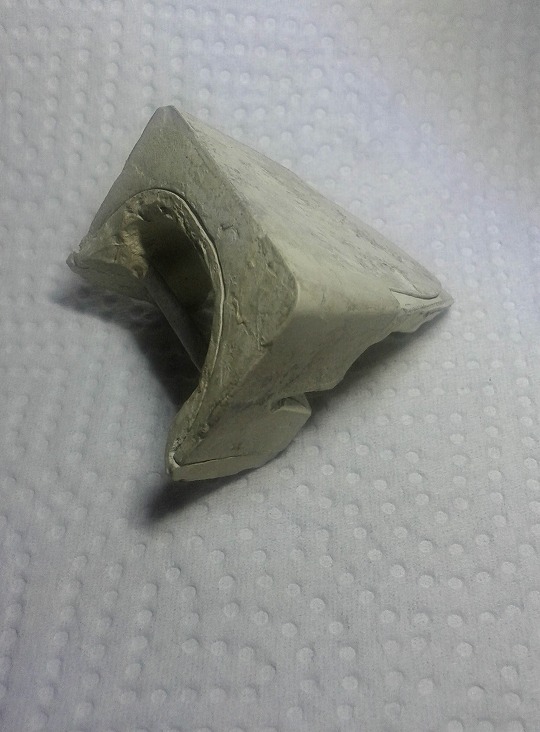
脱型は形状からも困難な事は想定内だったが
脱型時エポキシパテの型が無理をした結果割れたこともあり
都度、型の変形防止の補強やパテの厚みを増す補強を入れたりしている。
脱型は流線形状の部分と両端の薄い箇所を剥離し流線形の個所を剥していく。
薄い両端の上部から精密カッターの刃を打ち込んで徐々に剥していくが
パテは効果が始まってすぐぐらいの時期に始める事・・
パテは型から剥した段階では柔軟性がる為、若干の変形をしながらも型から剥離する事が出来るのだ。
薄い両端の上部から精密カッターの刃を打ち込んで徐々に剥していくが
パテは効果が始まってすぐぐらいの時期に始める事・・
パテは型から剥した段階では柔軟性がる為、若干の変形をしながらも型から剥離する事が出来るのだ。
よって脱型後の型は若干の変形を伴っているので 再び型にはめリードケースに型事はめ込み、完全硬化まで半日ほど待たなければならない・・
数回にパテを盛るのにも要領があり、型を抜くのにもタイミングが有り何事もそうだが慣れが必要だった・・・
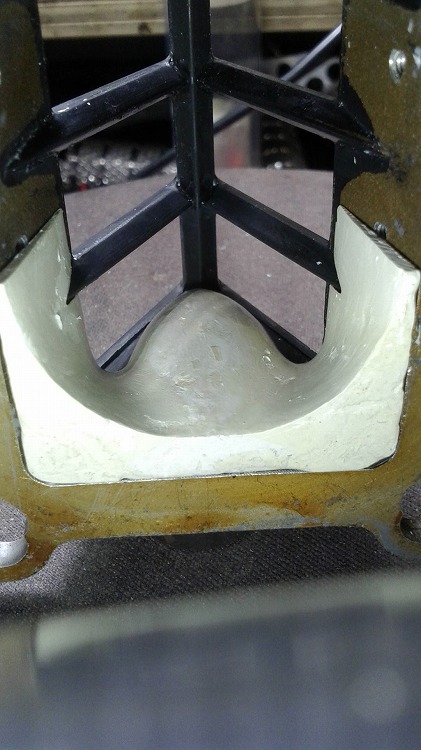
左右の中間部分に開先加工を行い接着しろを作り
エポキシパテを押し込み完全硬化を待つのである・・
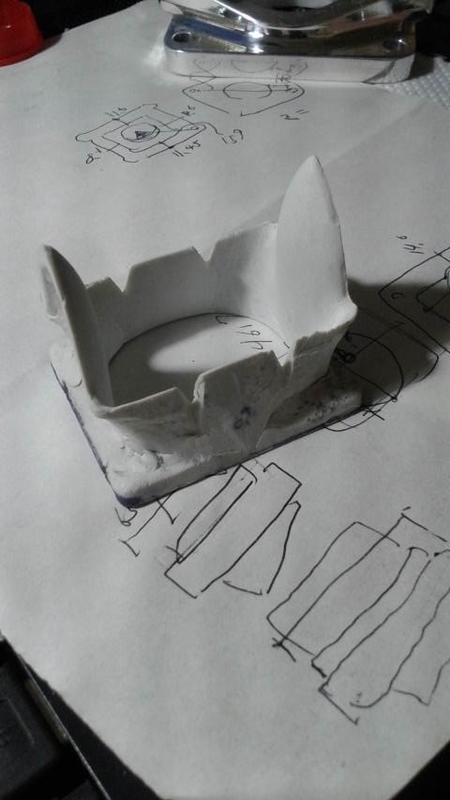
多分一個完成させるのにインテーク側とリードケースに合わせた微調整も含め3日以上かかったと思う?・・・